nR NEST HiLo 1:1 Roof Prototype
PROJECT DATA |
---|
TYPE | RESEARCH, CONSTRUCTION INNOVATION |
---|---|
LOCATION | ETH ZURICH, SWITZERLAND |
CLIENT | ETH ZURICH + EMPA |
PROJECT AND RESEARCH LEADS | BLOCK RESEARCH GROUP [BRG] A/S ARCHITECTURE AND BUILDING SYSTEMS ETH ZURICH |
PROFESSIONAL ENGINEERS | BOLLINGER+GROHMANN |
GENERAL CONTRACTOR | MARTI AG BAUUNTERNEHMUNG |
CONCRETE SPRAYING | BÜRGIN CREATIONS |
CONCRETE | HOLCIM SCHWEIZ AG |
CONCRETE STRUCTURAL TESTING | INSTITUTE OF STRUCTURAL CONCRETE RWTH AACHEN |
CABLENET COMPONENTS | JAKOB ROPE SYSTEMS LEHMANN TRUBB |
SCAFFOLDING | DOKA SCHWEIZ AG |
DATE | 2016 — 2017 |
TEAM | DAVE PIGRAM IAIN MAXWELL OLIVER BENNETT |
IMAGES | NAIDA ILJAZOVIC MICHAEL LYRENMANN URSULA FRICK DAVE PIGRAM OLIVER BENNETT |

NEST HiLo 1:1 Roof Prototype
ETH Zurich, Switzerland
nR
The cutting edge of the possible.
This full-scale experiment investigates the feasibility of spraying a textile reinforced thin concrete shell using a lightweight flexible formwork composed of a tensioned cablenet as falsework and tailored fabric as shuttering. This one-to-one prototype (within a bounding box of 20m x 10m x 7m) was undertaken as a dress rehearsal within a largely controlled environment ahead of the ultimate in-situ construction of the NEST HiLo project itself.
The development of the prototype focused on the first layer of NEST HiLo's thin concrete shell and represents a key milestone for the project, as it demonstrates the viability of the proposed lightweight, flexible formwork system to form a complex concrete structure. The prototype was built with the following objectives:
01 — To develop and test the cable net components at real scale.
02 — To test the feasibility of the system and the on-site logistics.
03 — To test the concrete spraying of a large and doubly-curved surface through the carbon-fibre reinforcement.
SM practice director Dave Pigram was research lead and managed the design, planning and construction of the roof prototype with documentation support from the Sydney office whilst on secondment to the Block Research Group [ETH Zurich].
NEST HiLo Roof Prototype
ETH Zurich, Switzerland
ETH Zurich, Switzerland
Construction Sequence Drawings
01
Setout Constraints
Minimum headrroom
Possible touchdown zones
02
NEST HiLo Roof in context
03 — 06
Steel Supports for roof touchdowns
Prototype Support Scaffold
Timber edge-beam
Tensile scaffold alternative
(if space had permitted)
07 — 10
Cablenet Geometry
Residual Forces
Cable thickness distribution
Node size distribution
11 — 14
Digital total station scanning
Scan 01 - Initial accuracy
Perimeter retensioning
Scan 02 - Increased accuracy
15 — 17
Fabric shuttering
Edge clamp
Carbon-fibre reinforcement
18 — 20
Spray sequence
21
Final Shell
01
Setout Constraints
Minimum headrroom
Possible touchdown zones
02
NEST HiLo Roof in context
03 — 06
Steel Supports for roof touchdowns
Prototype Support Scaffold
Timber edge-beam
Tensile scaffold alternative
(if space had permitted)
07 — 10
Cablenet Geometry
Residual Forces
Cable thickness distribution
Node size distribution
11 — 14
Digital total station scanning
Scan 01 - Initial accuracy
Perimeter retensioning
Scan 02 - Increased accuracy
15 — 17
Fabric shuttering
Edge clamp
Carbon-fibre reinforcement
18 — 20
Spray sequence
21
Final Shell
360° Walkthrough Tour
Virtual tour of roof prototype by Zitronenwolf.
01
Cable Net
02
Fabric Formwork
03
Final Shell
Virtual tour of roof prototype by Zitronenwolf.
01
Cable Net
02
Fabric Formwork
03
Final Shell
Cablenet
The doubly-curved form of the roof is defined by a network of rods and cables stretched under tension. This system allows for the realisation of complex curvature with far less material and wastage.
The doubly-curved form of the roof is defined by a network of rods and cables stretched under tension. This system allows for the realisation of complex curvature with far less material and wastage.

Fabric Shuttering from Below
The cablenet is covered with a tailored geotextile fabric shuttering.
It is this surface that supports and gives form to the shotcrete subtly bulging between the cables and revealing the pattern of thier alignents.
The cablenet is covered with a tailored geotextile fabric shuttering.
It is this surface that supports and gives form to the shotcrete subtly bulging between the cables and revealing the pattern of thier alignents.

Fabric Shuttering from Above
The overall form of the shell is defined by the shape of the timber edge-beam, by the unique length of each cable segment and by the specififc tension applied at the ends of each cable row.
The upperside of the fabric shuttering reveals the seams of the patterned fabric, and the spacers that will support the carbon-fibre reinforcement.
The overall form of the shell is defined by the shape of the timber edge-beam, by the unique length of each cable segment and by the specififc tension applied at the ends of each cable row.
The upperside of the fabric shuttering reveals the seams of the patterned fabric, and the spacers that will support the carbon-fibre reinforcement.

Concrete Spraying
The concrete is applied by two teams of two. Each team has one member to spray the concrete to the approproate thickness and one to use a vibrating trowel to ensure that the concrete flows in and around the carbon fibre mesh reinforcement.
The spraying must follow a specific sequence so that the cablenet sags as planned under the 19 tons of concrete.
The concrete is applied by two teams of two. Each team has one member to spray the concrete to the approproate thickness and one to use a vibrating trowel to ensure that the concrete flows in and around the carbon fibre mesh reinforcement.
The spraying must follow a specific sequence so that the cablenet sags as planned under the 19 tons of concrete.

Construction Sequence
ETH Zurich
ETH Zurich
Shell With Flexible Formwork Removed
01
Test installation of the hydronic heating and cooling pipework to the upper side of the shell.
02
The underside of the shell reveals the pillowed imprint of the cablenet and fabric shuttering in turn revealing the flow of forces between touchdowns.
01
Test installation of the hydronic heating and cooling pipework to the upper side of the shell.
02
The underside of the shell reveals the pillowed imprint of the cablenet and fabric shuttering in turn revealing the flow of forces between touchdowns.


Selected Publications
01
Beyond Bending
Edition Detail, Germany
02
Robust Resilient Resistant
Edition Detail, Germany
03
An Ultra-Thin Double-Curved Concrete Roof
Architect, USA
04
Ultrathin concrete roof to cap a net-positive energy rooftop apartment
Architect’s Newspaper, USA
05
Bauwelt: Digital Fertigan [Digital Fabrication]
German
06
The Structural Engineer
Special Issue: 2024 Vision
07
Azure
The high-tech future of concrete
08
The Economist
UK/International Edition
01
Beyond Bending
Edition Detail, Germany
02
Robust Resilient Resistant
Edition Detail, Germany
03
An Ultra-Thin Double-Curved Concrete Roof
Architect, USA
04
Ultrathin concrete roof to cap a net-positive energy rooftop apartment
Architect’s Newspaper, USA
05
Bauwelt: Digital Fertigan [Digital Fabrication]
German
06
The Structural Engineer
Special Issue: 2024 Vision
07
Azure
The high-tech future of concrete
08
The Economist
UK/International Edition

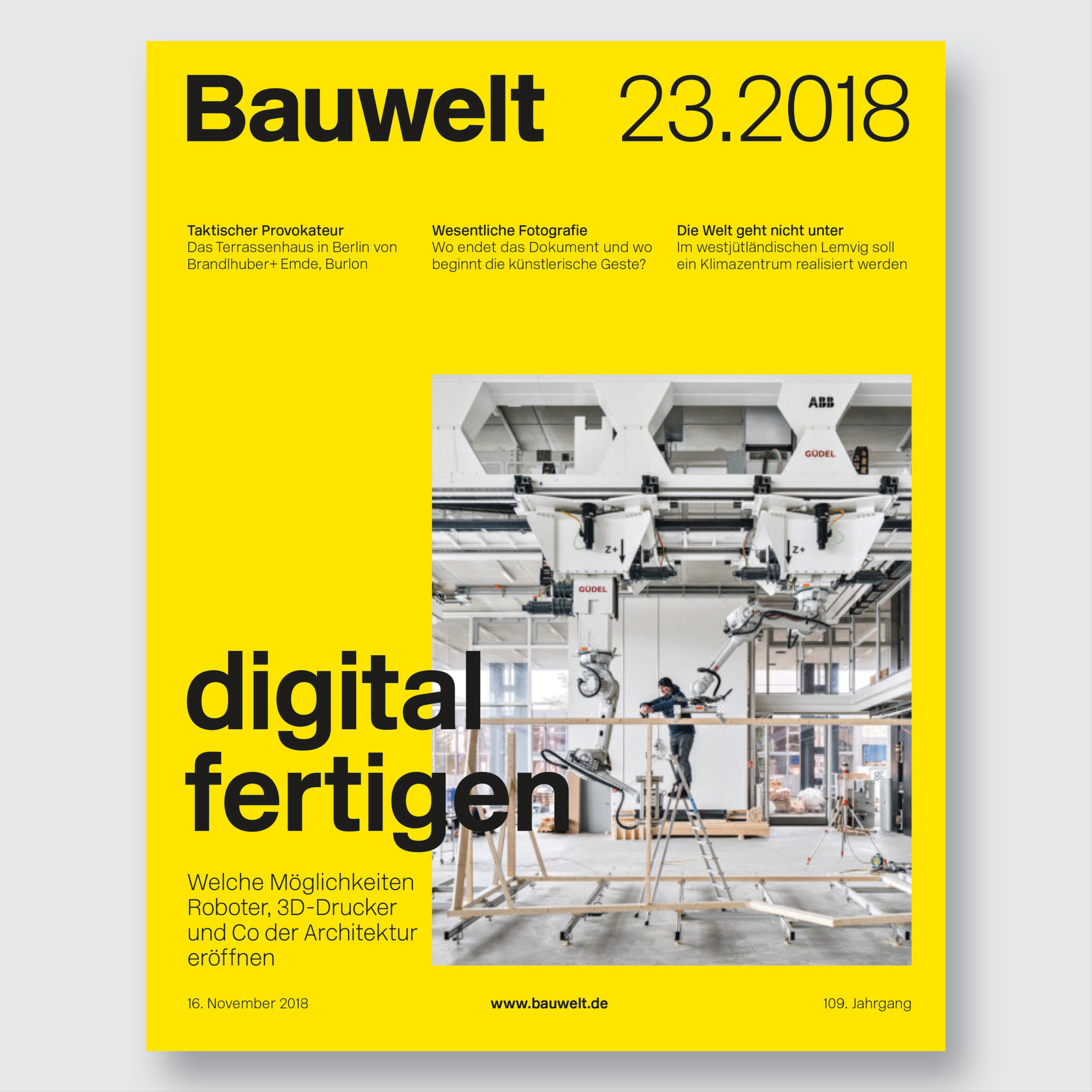


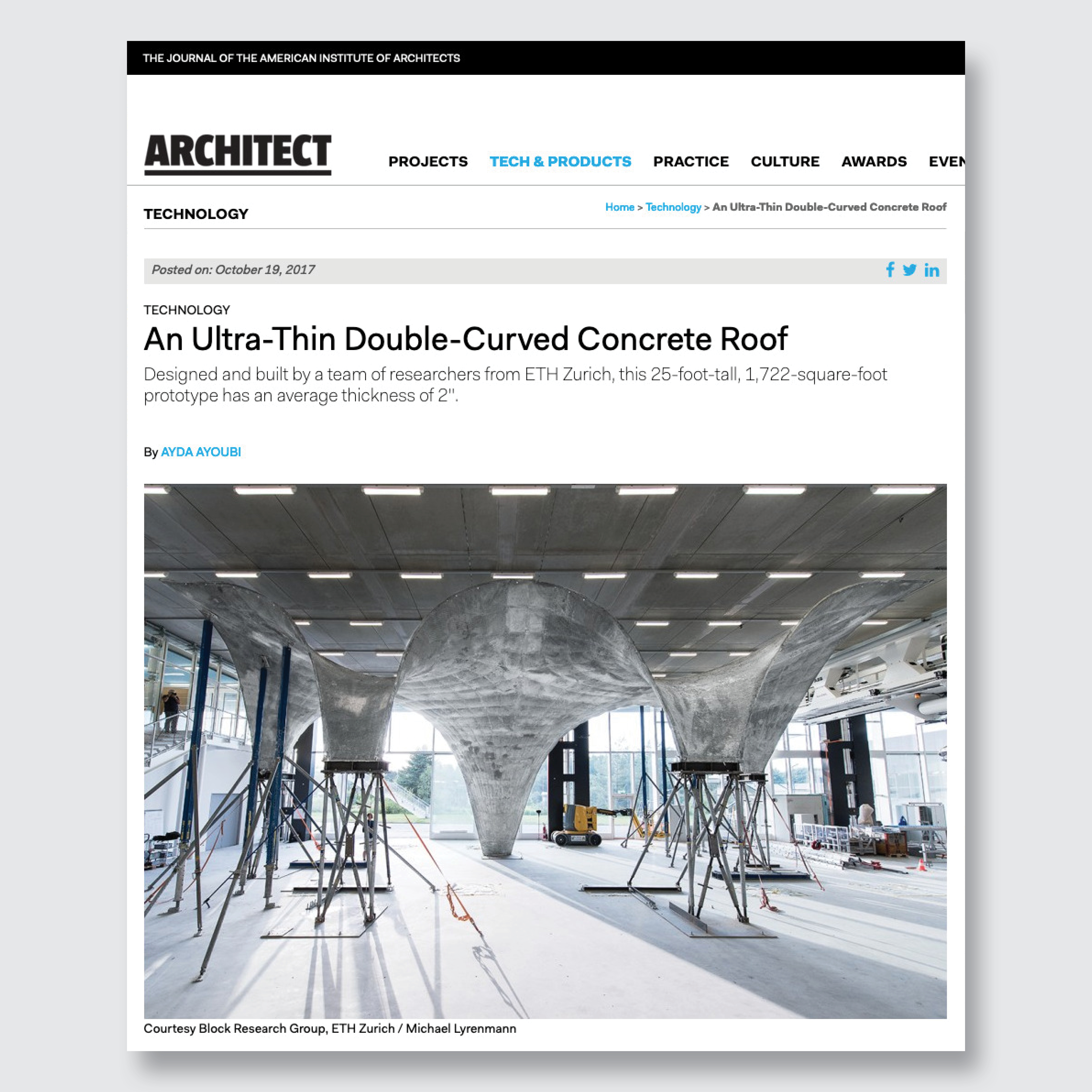



Final Roof Prototype
The dramatic form and extreme thinness of the roof along with the pillowed imprint of its fabrication method is revealed.
