rV ReVault
PROJECT DATA |
---|
TYPE |
PAVILION |
---|---|
REVAULT 1.0 LOCATION |
ANN ARBOR, MICHIGAN, USA |
REVAULT 1.0 CLIENT | MATTHAEI BOTANICAL GARDENS & NICHOLS ARBORETUM |
DATE | rV 2.0 — 2024 rV 1.0 — 2010 |
TEAM | DAVE PIGRAM IAIN MAXWELL |
REVAULT 1.0 COLLABORATORS | WES MCGEE [MATTER DESIGN] MACIEJ KACZYNSKI |
PHOTO | WES MCGEE |
AWARDS |
RESEARCH THROUGH MAKING GRANT TAUBMAN COLLEGE OF ARCHITECTURE & URBAN PLANNING UNIVERSITY OF MICHIGAN |
PUBLICATIONS |
ROBOTIC FABRICATION IN ARCHITECTURE ART AND DESIGN 2014 |

ReVault 2.0
Ann Arbor, Michigan, USA
rV
A pair of pavilions that showcase the spatial potential of an innovative design-material system combining fabrication-aware computational form-finding techniques with low-carbon masonry structures enabled via automated robotic waterjet fabrication.
ReVault 2.0 explores the realisation of complex masonry vault and shell structures through the development of computational form-finding strategies coupled to robotic fabrication techniques.
The project revisits historical stone construction techniques that utilised shaped stones — i.e. voussoirs — to efficiently transmit compressive forces. Traditionally, such structures utilised less-efficient circular arch forms to simplify the work of the mason through the provision of repetitive parts. Here, our realisation of digital file-to-factory protocols aided by automated fabrication, allows for the pursuit of more complex and efficient shell structures. Further, the unique ruled-edges of the hexagonal masonry elements aids assembly by directing part alignment and reducing the amount of temporary falsework required to support the incomplete assembly during construction.
Our research spans three key activities:
01 — The creation of bespoke digital design software that embeds the constraints of the material system [panel size relative to curvature; panel alignment relative to force flow; minimum contact surface-area at joints] and water-jet fabrication method [geometric limits for element size and cutting angles required for edge shaping] within the generative protocols [i.e. compression-only form-finding] of the pavilion design itself.
02 — Expansion of our custom robot control ecosystem — SuperMatterTools — to enable pose, toolpathing and simulation of the water-jet fabrication method.
03 — The design of all hardware and safety systems necessary to mount a proprietary water-jet cutter to a Kuka KR120HA industrial robotic arm.
Revault 2.0 [2024] revisits the original Re-Vault [2010-11] project and research collaboration with Wes McGee [Matter Design] and Maciej Kaczynski supported by a Research Through Making Grant awarded by the University of Michigan, Taubman College of Architecture and Urban Planning.
The project revisits historical stone construction techniques that utilised shaped stones — i.e. voussoirs — to efficiently transmit compressive forces. Traditionally, such structures utilised less-efficient circular arch forms to simplify the work of the mason through the provision of repetitive parts. Here, our realisation of digital file-to-factory protocols aided by automated fabrication, allows for the pursuit of more complex and efficient shell structures. Further, the unique ruled-edges of the hexagonal masonry elements aids assembly by directing part alignment and reducing the amount of temporary falsework required to support the incomplete assembly during construction.
Our research spans three key activities:
01 — The creation of bespoke digital design software that embeds the constraints of the material system [panel size relative to curvature; panel alignment relative to force flow; minimum contact surface-area at joints] and water-jet fabrication method [geometric limits for element size and cutting angles required for edge shaping] within the generative protocols [i.e. compression-only form-finding] of the pavilion design itself.
02 — Expansion of our custom robot control ecosystem — SuperMatterTools — to enable pose, toolpathing and simulation of the water-jet fabrication method.
03 — The design of all hardware and safety systems necessary to mount a proprietary water-jet cutter to a Kuka KR120HA industrial robotic arm.
Revault 2.0 [2024] revisits the original Re-Vault [2010-11] project and research collaboration with Wes McGee [Matter Design] and Maciej Kaczynski supported by a Research Through Making Grant awarded by the University of Michigan, Taubman College of Architecture and Urban Planning.
Light and Shade
The form of the pavilion incorporates three internal ‘teardrop’ openings that deliver light and water to their accompanying gardens. and provide sharply contrasting areas of light and shade.
The form of the pavilion incorporates three internal ‘teardrop’ openings that deliver light and water to their accompanying gardens. and provide sharply contrasting areas of light and shade.

Custom Software
Fabrication-aware form-finding embeds the constraints of making — part size, fixturing and geometric limits — into the generative processes of form-finding, Here custom written algorithms define compression-only forms appropriate to production in sandstone in concert with defining stone voissoirs that can be robotically waterjet cut.
Fabrication-aware form-finding embeds the constraints of making — part size, fixturing and geometric limits — into the generative processes of form-finding, Here custom written algorithms define compression-only forms appropriate to production in sandstone in concert with defining stone voissoirs that can be robotically waterjet cut.
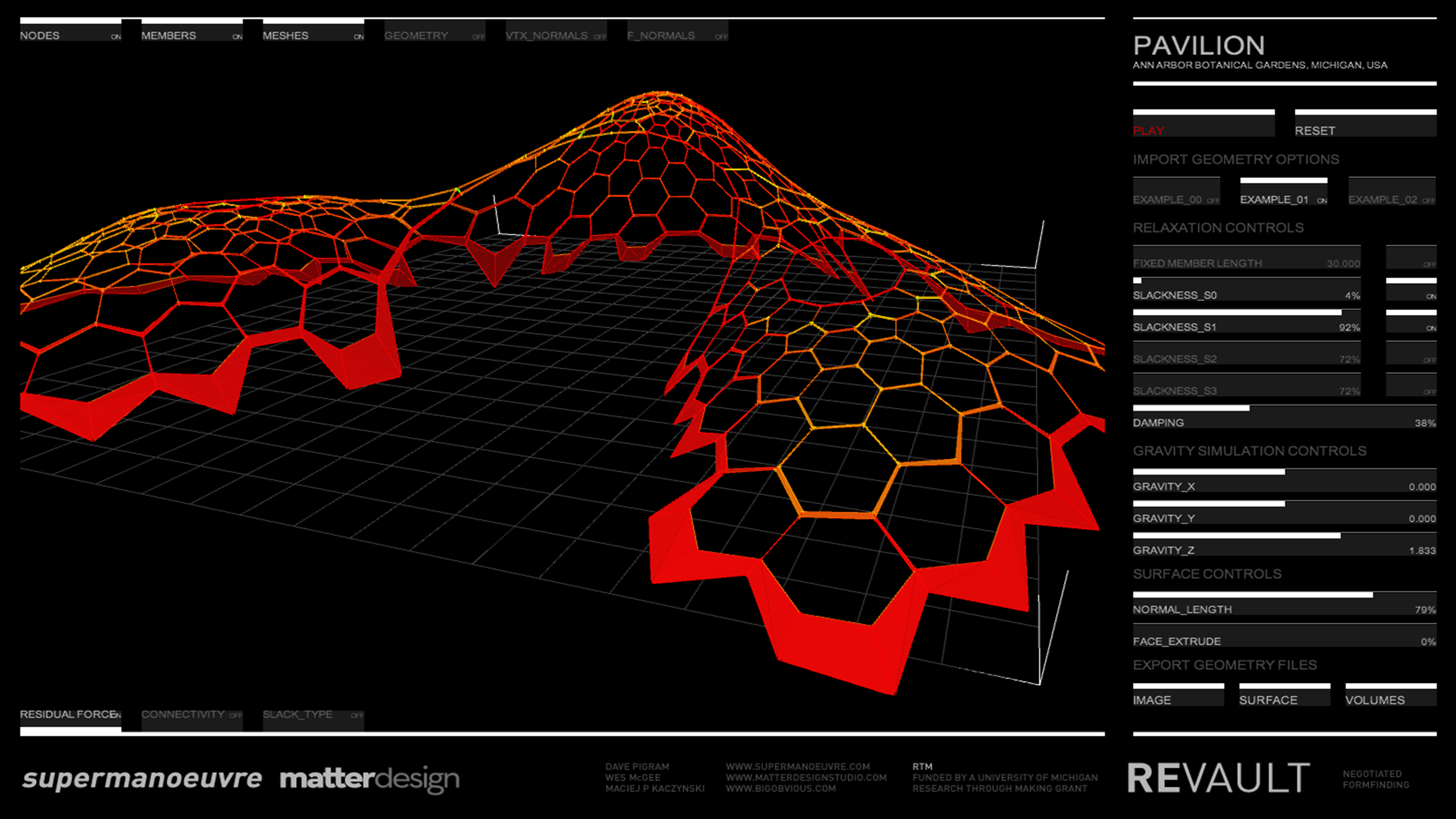
Assembly
The dry-stack elements feature twisting ruled-surface edge-interfaces to aid alignment and allow for temporary cantilevering during construction.
This minimises the need for precise falsework, instead requiring only reusable propping. This radically reduces the waste traditionally associated with stone vaults, especially irregular structurally-optimised vaults.
The dry-stack elements feature twisting ruled-surface edge-interfaces to aid alignment and allow for temporary cantilevering during construction.
This minimises the need for precise falsework, instead requiring only reusable propping. This radically reduces the waste traditionally associated with stone vaults, especially irregular structurally-optimised vaults.
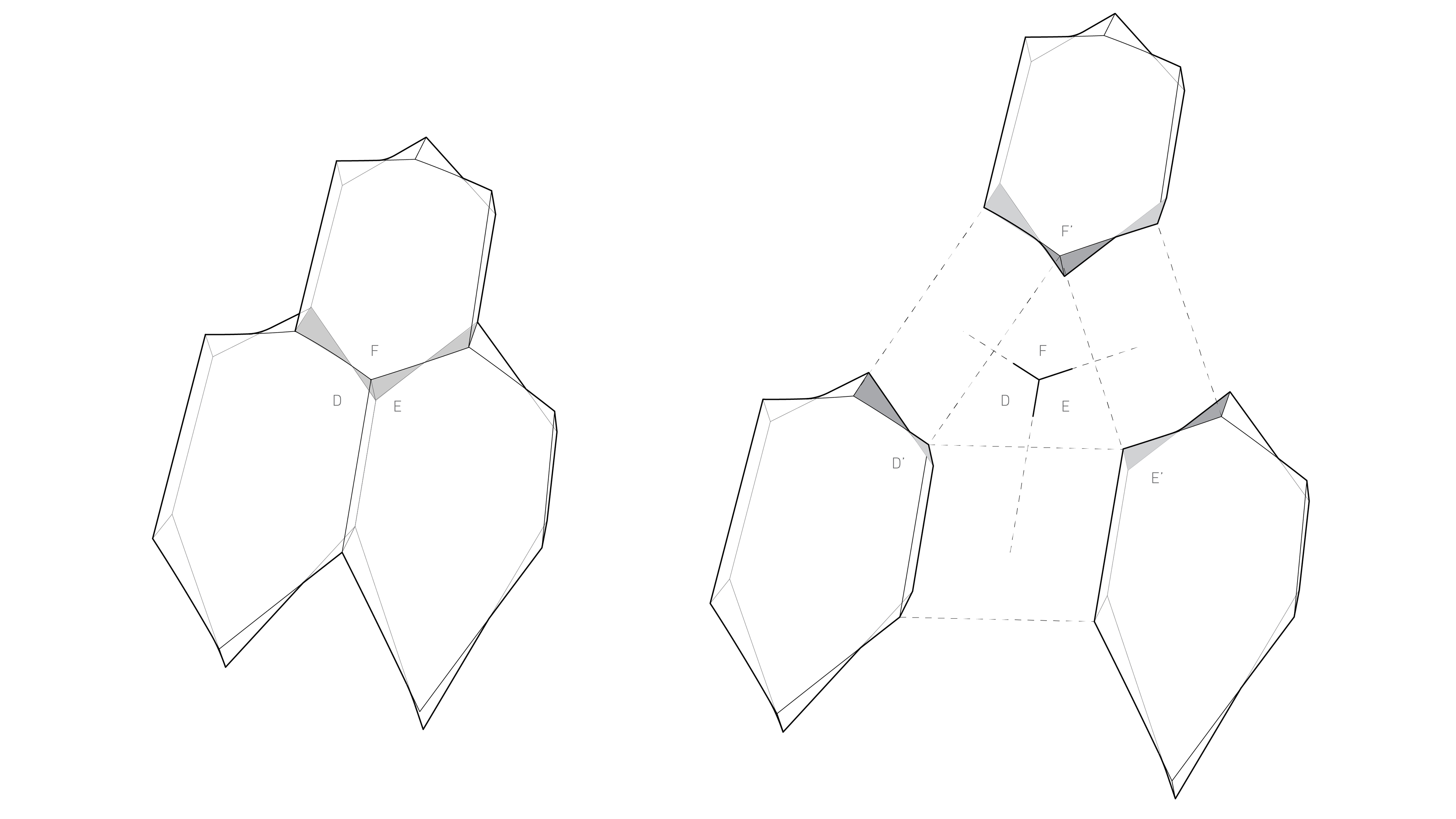
Robotic Waterjet Cutting
Each stone voissoir is unique, digitally cut to match perfectly with its neighbours. The global form is embeeded in the form of its constitent parts removing the need for complete falsework.
Each stone voissoir is unique, digitally cut to match perfectly with its neighbours. The global form is embeeded in the form of its constitent parts removing the need for complete falsework.


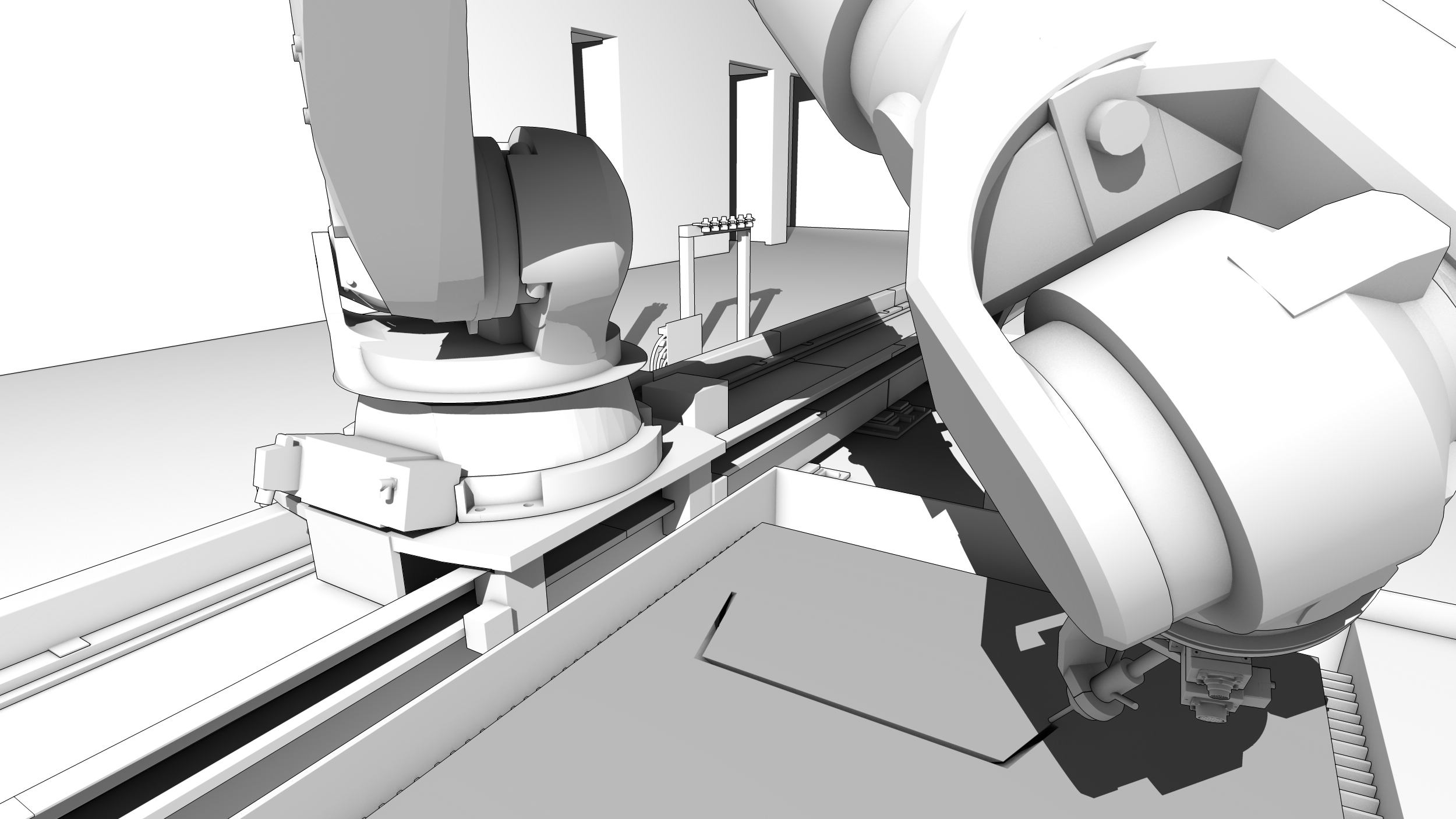
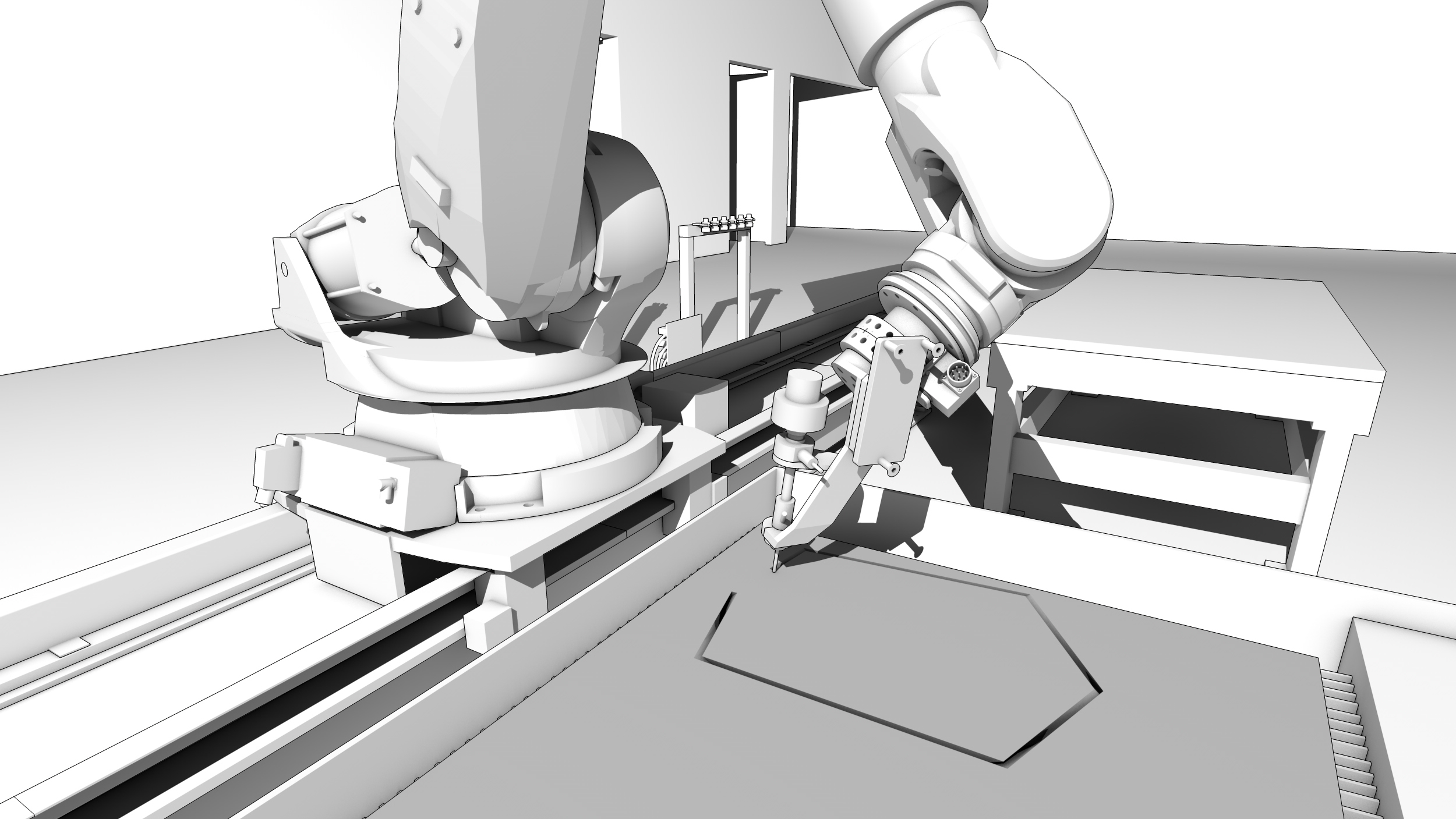
Twisted Edges
The twisting contact surfaces at the top and bottom of each voissoir are a key innovation of this material-system. The twist provides an additional aspect of joint interlock adding to the course interlock that results from the point-down hexagonal block geometry. Together, the two interlocking mechanisms allow each additional block to cantilever from those that preceed it further reducing falsework due to lessened support requirements.
The twisting contact surfaces at the top and bottom of each voissoir are a key innovation of this material-system. The twist provides an additional aspect of joint interlock adding to the course interlock that results from the point-down hexagonal block geometry. Together, the two interlocking mechanisms allow each additional block to cantilever from those that preceed it further reducing falsework due to lessened support requirements.
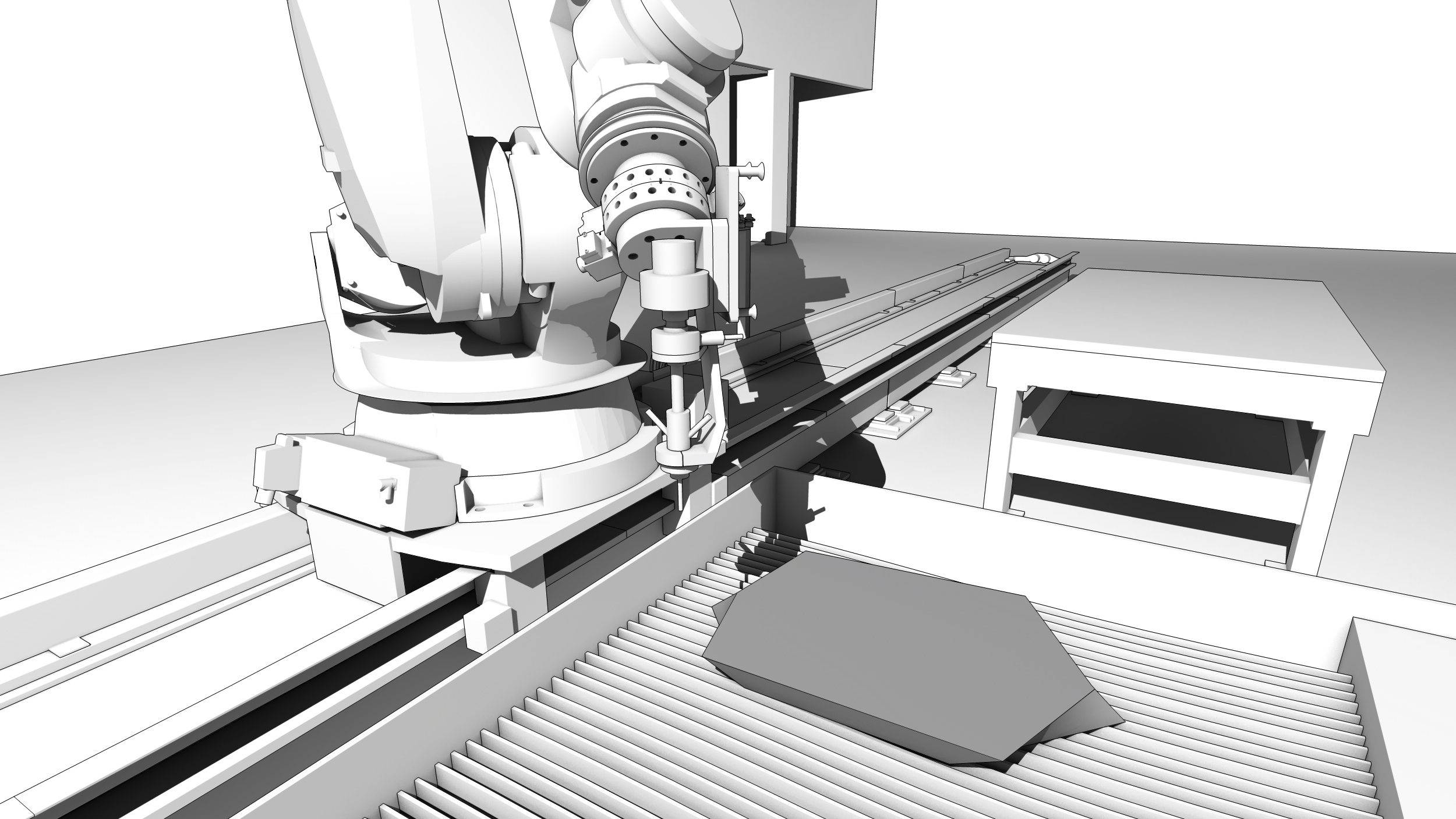
Structural Analysis
Finite Element Analysis [FEA] of dry stack hexagonal shell elements completed in ANSYS.
01
Equivalent Stress
Red = Maximum [79.571 psi]
Blue = Minium [0.021 psi]
02
Total Deformation
Red = Maximum [0.007 inches]
Blue = Minium [0.000 inches]
03
Vector Principal Stress
Red = Maximum Principal
Blue = Minium Principal
Finite Element Analysis [FEA] of dry stack hexagonal shell elements completed in ANSYS.
01
Equivalent Stress
Red = Maximum [79.571 psi]
Blue = Minium [0.021 psi]
02
Total Deformation
Red = Maximum [0.007 inches]
Blue = Minium [0.000 inches]
03
Vector Principal Stress
Red = Maximum Principal
Blue = Minium Principal
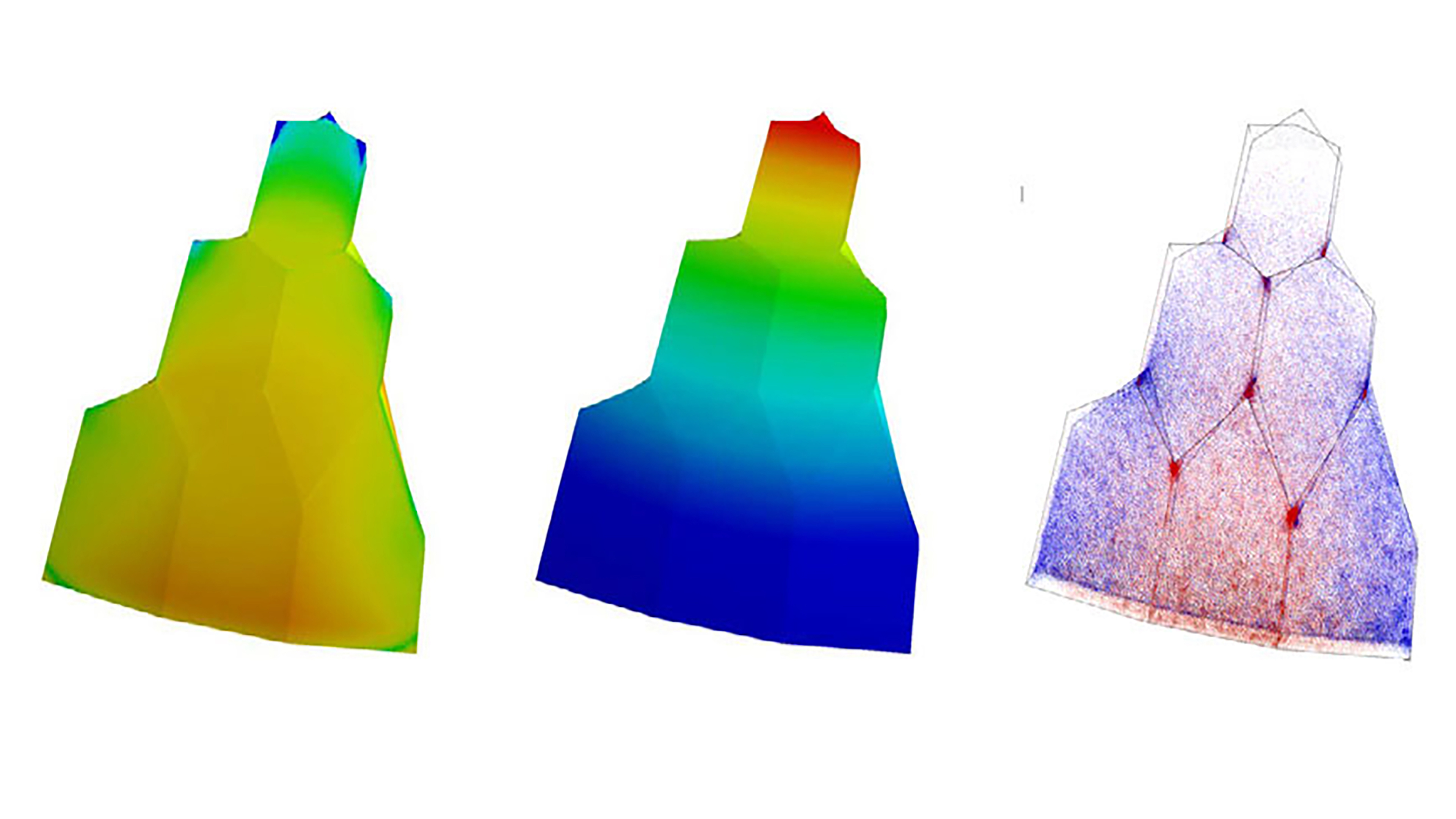
1:1 Dry stone mock-up
Detail highlighting swept water-jet cut edges
Detail highlighting swept water-jet cut edges

Gardens and Touchdowns
Gardens intergated within raised planters and touchdowns form a symbiotic relationship. All touchdowns land in, and channel water into, gardens within raised planter beds. The inner ‘teardrop’ touchdowns reduce the overall span of the vault and create more diverse lighing conditions suited to understorey planting. The gardens humidify the air, support biodiversity and provide a literal and symbolic barrier to prevent climbing.
Gardens intergated within raised planters and touchdowns form a symbiotic relationship. All touchdowns land in, and channel water into, gardens within raised planter beds. The inner ‘teardrop’ touchdowns reduce the overall span of the vault and create more diverse lighing conditions suited to understorey planting. The gardens humidify the air, support biodiversity and provide a literal and symbolic barrier to prevent climbing.

Shingle-like Surface and Stepped Edges
The exposed edges of the pavilion reveals the slight thickening of the stone towards the ground in direct response to the accumulation of loads. The vault’s stepped surface and edges result from the shingle-like positioning of planar stone elements on its dramatically doubly-curved form. The non-smooth surface creates an ever-changing swarm of shadows and highlights that evidence and amplify awareness of the passing of time.
The exposed edges of the pavilion reveals the slight thickening of the stone towards the ground in direct response to the accumulation of loads. The vault’s stepped surface and edges result from the shingle-like positioning of planar stone elements on its dramatically doubly-curved form. The non-smooth surface creates an ever-changing swarm of shadows and highlights that evidence and amplify awareness of the passing of time.
